How to Properly Perform Roofing Installation
A home’s roof keeps it protected from rain, snow, sunlight, and other harsh weather conditions. It also adds a lot to its overall look and design.
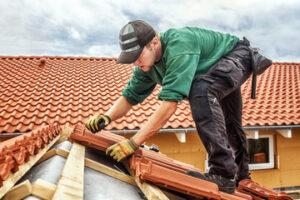
If your roof shows signs of deterioration, you may want to consider re-roofing. Re-roofing is a lot less expensive than a full replacement, but still requires a lot of work. Contact Ellingson Roofing LLC for professional help.
Before shingles or any other roofing materials are installed, it’s important to have an underlayment layer that acts as an additional barrier against water infiltration. Roofing underlayment is a waterproof or water-resistant material that gets fixed directly to your roof deck before other roofing materials are applied. It helps prevent moisture from infiltrating your roof and it helps to support the work of the shingles, as well.
There are three primary types of roof underlayment: felt, synthetic, and rubberized asphalt. Each type has different characteristics and may be more suitable for certain roofing materials or environmental conditions. Choosing the right underlayment depends on a variety of factors, including cost, durability, and weather resistance. Consulting with a licensed roofing professional is the best way to determine which underlayment is the best fit for your project.
Felt underlayment is one of the oldest and most common types of roofing underlayment. It’s created by saturating paper or mat with asphalt, which is then laminated together. It’s available in a variety of weights, from No. 15 to No. 30, and is usually rolled out to the edges of the roof, with a slight overlap per manufacturer instructions.
Synthetic underlayment is a more modern option that started to become popular about a decade ago and is still the most common choice among homeowners. It’s made from various polymers that have been woven together and it’s often backed with butyl-based or rubberized adhesive. It’s a bit more expensive than felt underlayment, but it performs better in high-temperature environments and provides an extra layer of protection against the elements.
Rubberized asphalt underlayment is a more recent product that features an asphalt and rubber polymer blend that makes it extra waterproof. It’s often used in valleys, around penetrations, and other areas where moisture is a concern.
Shingles
After the underlayment and leak barrier are in place, it’s time to lay shingles. Before you do, check that the roof decking is in good shape and free of soft or rotted areas. This is important since any shingle installation mistakes could result in water leaks into your home.
If you’re doing the shingle installation yourself, start by clearing the work area and removing any debris that might pose tripping hazards. If you have plants or garden beds close to the house, cover them with sturdy tarps to protect them from dropped tools and falling shingles. Pull any yard games or furniture away from the house, too. This will make it easier to access and work on the roof.
You’ll need to decide whether you’re going to use the racking or shingle-by-shingle method of installation. The racking method is faster because you can work steadily from left to right, filling a row at a time. The shingle-by-shingle method requires more careful planning and attention to detail, especially nail placement. It’s also important to plan ahead and choose a clear day for your roofing project; working in wet weather can lead to disaster.
If your roof has valleys, it’s important to complete the metal valley flashing before you begin laying shingles. These are areas prone to leaks, and leaks can occur anywhere the shingle layer is penetrated, interrupted or meets a wall. The shingle manufacturer will recommend which type of valley flashing to use, and you should follow the instructions on the product packaging. For longer roof performance, IKO recommends open valleys rather than closed valleys. To install a closed valley, a shingle course is installed on both sides of the valley first and then the end of each shingle is trimmed back 2” from the valley centerline. Then a second course of shingles is installed, and the end nails are trimmed back another 2” from the valley centerline.
Flashing
Flashing is a thin, impervious material (often made of metal) that seals joints and seams where roofing materials meet walls, chimneys, vents, skylights, and other protrusions. Without it, water can seep through these areas and wreak havoc in the home.
To prevent this, professional roofers install a series of flashings to create a waterproof barrier. These include channel flashing, a “U”-shaped piece that catches and diverts water where the edge of the roof meets a wall; apron flashing, a long, single strip that covers the joint between a vertical surface and a sloping roof (at the lower end of a chimney); valley flashing, which protects the middle section where two roof sections meet; and drip edge flashing, which carries rainwater to gutters or down the side of the house.
Other types of flashing include counterflashing, sheet metal that covers the top edges of base flashing run up a wall; kickout flashing, which helps water flow away from the wall and onto a gutter; and pipe flashing, which fits the cylindrical contour of pipes and other conduits. Flashing should be capped with a caulking or other waterproof sealant to prevent leaks.
To ensure a good flashing installation, a roofer should inspect and replace it as needed. Generally, flashing isn’t expected to last as long as the roof itself; but it is essential for keeping your home safe from leaks. To extend the life of flashing, homeowners should keep it free from debris and periodically check for damage or wear. In some cases, a roofer may choose to reuse old flashing during a re-roofing job. However, it’s best to replace all flashing at the time of a roof replacement to avoid potential issues in the future.
Gutters
Gutters are a vital part of any roof. They prevent water buildup that can ruin shingles and cause leaks in the interior of the home or foundation. They also direct rainwater away from the foundation, which helps preserve the integrity of a house’s structural base.
Gutters start at the eave of the roof and channel water into downspouts that are directed away from the foundation. They also help prevent soil erosion that can damage landscaping and greenery near the house, as well as reduce the amount of water that seeps into crawl spaces and basements.
Before you install the gutter, carefully measure each section of your roofline to determine how much material you will need. Make sure you have enough length to complete the job, as well as extra length for connecting gutter pieces and end caps. To ensure that you’re installing the gutter at a proper angle, mark a chalk line along the fascia board where it will start to indicate how much of a slope your gutter should be. Typically, you want to have a slight slope of 1/8 inch per foot toward the downspout location.
The gutter system is made up of a trough, soffit, fascia and downspouts. A downspout is a vertical pipe that redirects the flow of water from the gutter to ground level or into a drainage system. The soffit is the underside of an eave, which runs along the roofline, and the fascia is the flat board that connects to the soffit and supports the gutter.
The gutter pieces come in different sizes to match the size of your roof, and they are available in steel or aluminum. Steel gutters are more durable than aluminum, and they withstand snowfall and hail better. They’re also rust-resistant and carry long, 25-year warranties. However, steel can be more expensive than aluminum.